When and why to simulate business processes
August 21, 2021
1569 words
8 minutes to read
Last Updated: September 4, 2021
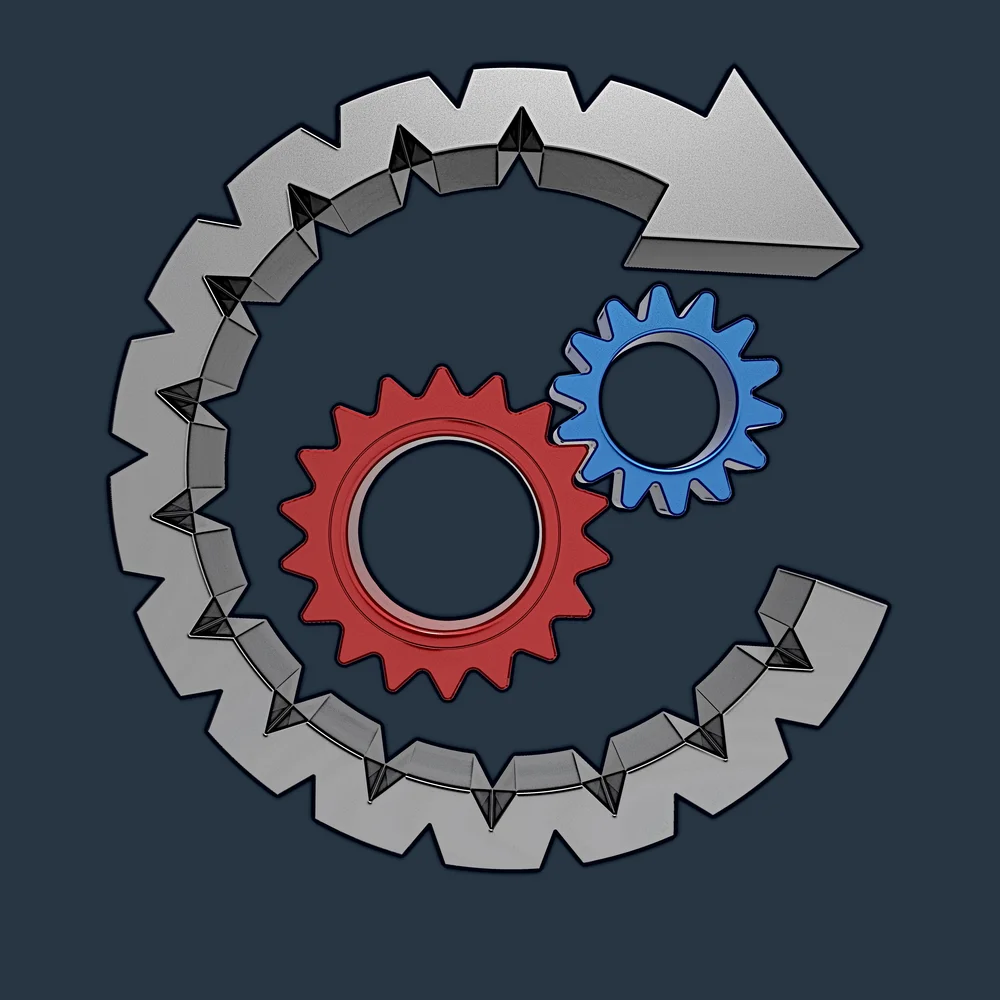
Numerous definitions have been proposed for the term simulation. Banks, et al. (2013) proposed an exceptionally thorough definition from Discrete-Event System Simulation:
Simulation is the imitation of the operation of a real-world process or system over time. Whether done by hand or on a computer, simulation involves the generation of an artificial history of a system and the observation of that artificial history to draw inferences concerning the operating characteristics of the real system.
The behavior of a system as it evolves over time is studied by developing a simulation model. This model usually takes the form of a set of assumptions concerning the operation of the system. These assumptions are expressed in mathematical, logical, and symbolic relationships between the entities, or objects of interest, of the system.
Once developed and validated, a model can be used to investigate a wide variety of “what if” questions about the real-world system. Potential changes to the system can first be simulated, in order to predict their impact on system performance. Simulation can also be used to study systems in the design stage, before such systems are built.
Thus, simulation modeling can be used both as an analysis tool for predicting the effect of changes to existing systems and as a design tool to predict the performance of new systems under varying sets of circumstances.
Although somewhat long, this definition touches upon nine significant factors for defining a simulation:
- imitation … of a real-world process or system over time;
- generation of an artificial history … and the observation of that artificial history;
- [drawing] inferences concerning the operating characteristics of the real system;
- [study of the] behavior of a system as it evolves over time;
- [models] … [taking] the form of a set of assumptions;
- assumptions … expressed in mathematical, logical, and symbolic relationships;
- [investigating] … “what if” questions about the real-world system;
- predicting the effect of changes to existing systems; and
- [predicting] the performance of new systems.
When, how, and why would simulation support decision-making for new or improved business processes? Critical business decisions are never simple, and most businesses do not possess the extensive experience necessary to answer even the seemingly simple questions in an objective, scientific way. Simulation is a productive method of solving process problems and making data-driven process decisions.
The pros and cons of using business process simulations will be described in this blog. We will also propose a rationale for using/not using business process simulations.
How can simulation help the team? The advantages of business process simulation
Mathematical analysis, (such as the use of queueing models, queueing networks, Markov chains, and stochastic Petri nets), is much less detailed and implements fewer limitations. Analytical modeling should be used instead of simulations if simplicity is the overriding factor.
Compared to real-world experimentation, simulation has a number of remarkable advantages – more below. Understanding these advantages will allow the team to better discern the critical value propositions of simulations.
1. Reduce costs and time to implementation
If all the details for a new or changed process are known, then the team can simply follow a few simple steps to assess the cost of implementation. However, a simulation will lead to a finalized plan that will more accurately determine how to bring the proposed changes into the real-world and how to allocate the range of resources that implementation will demand. Moreover, the team will be able to reduce the risk of unexpected challenges, unreasonable downtime, or catastrophic business process interruptions.
2. Evaluate scenarios without disrupting operations
Simulation enables a team to test changes to a process without disrupting it. Real-world operations carry on, while the changes are appraised in a standalone simulated environment. Of course, this is especially useful with business-critical processes that must remain up and running at all times.
Aside from allowing an organization to keep operational systems working, business process simulation safeguards the organization from the potentially negative consequences of the suggested changes. Mistakes, miscalculations, or overlooked details in a virtual environment cannot affect the efficiency and performance of the real-world system. Thus, simulation enables a team to test ideas safely and exhaustively before releasing them live into the work environment.
3. Allocate optimal resources
Does the team have enough resources – more specifically, time, staff, and money – to be able to evaluate the consequences of every possible parameter change in a business process? The team most likely does not – even if the team did, simulation can help avoid spending ridiculous amounts of money on testing all conceivable outcomes.
Time remains an issue with simulation to some extent (since the team needs to define and test models), but the team won’t need to worry about constrained resources in a simulated environment as much. For example, if the changes to a business process imply the purchase of new hardware, a simulation could facilitate testing the impact of the hardware on operations without actually purchasing it.
4. Test a wide range of ideas
Simulation is flexible and significantly facilitates the testing of a wide range of questions. Simulation can stimulate creativity and “process thinking.” By changing the input data and parameters of a model, the team can quickly assess how it performs under different conditions. Aside from that, business process simulation allows the team to identify and throw away unrealistic, unsustainable ideas and focus on the ones that have real potential to improve the business’s operations.
5. Identify shortcomings and bottlenecks
Simulation can communicate ideas efficiently and effectively. Every parameter change – regardless of how insignificant it seems – may lead to unpredictable behavior in the system. Simulation can help pinpoint not only the advantages but also the inefficiencies and bottlenecks caused by the performed adjustments to the model.
Simulation permits a large number of questions to be answered. Simulation allows the team to identify side effects and quickly make improvements to ensure that the model is suitable for the business goals of the enterprise.
6. Assess the effects of the changes from real-world data
With business process simulation, the team can obtain hard data as to how different scenarios will impact operations. First of all, the team can perform a more reliable and validated cost-benefit analysis. Second, benefits proposed improvements to managers and stakeholders can be more easily demonstrated. Ultimately, business process simulation can prevent organizational hurdles by winning over key decision-makers with demonstrable results.
When to employ business process simulation
The benefits of business process simulation should be clear by now. That’s just part of the story, though. How does the team know if a simulation is the best course of action for the situation?
Well, business process simulation would be an optimal choice in the following cases:
- Uncertainty exists as to how the target system will behave after the changes.
- Resource constraints in the operational system will not permit the testing of a wide range of ideas or answering a significant number of questions.
- Every detail in a plan must be taken into consideration.
- Real-world business processes cannot be stopped or interrupted in order to improve them.
- Managers and stakeholders will only approve changes when they are presented with credible data about the outcomes of different ideas.
There may be many other cases where simulation would be preferable to real-world experimentation.
To summarize, the team should consider using simulation anytime real-world testing is impractical. Considering that modern business processes can be exceptionally complex, a simulation could be immeasurably useful in just about any situation.
When simulation should not be used
Simulation isn’t always the ideal tool for the job. Even though the rules proposed by Banks and Gibson (1997) are over 30 years old, they are still relevant to business simulations today:
- The problem can be solved using “common sense analysis”.
- The problem can be solved analytically, such as steady-state queing models, probabilistic inventory models, and others that can be solved using equations in a closed form.
- Direct experiments on the real system are easier to perform than setting up the simulation.
- The cost of the simulation exceeds possible savings.
- The project lacks appropriate resources, i.e., people, data, or time.
- Limited time is wanting for the model results to be useful.
- No data-not even estimates-are available.
- The model can’t be verified or validated due to the lack of people, data, or time.
- Project expectations can’t be met for the decision-makers.
- The system behavior is too complex, or can’t be defined.
Next steps
Business process simulation is undeniably a useful instrument, but it requires careful conceptualization and implementation. Simulations are not magical tools that can effortlessly solve any problem thrown at them. To set up the foundation for success, the team needs to formulate solutions to the intended issues and questions. The process to be improved needs to be understood well enough for accurate modeling.
Consider incorporating steps like choosing a probability distribution to represent input data and validating your model to assess its usefulness. Simulation can be a complex process that must be meticulously planned. But if the approach is methodological, the team will be able to uncover the potential of business process simulation to its full extent.
References:
Banks, J., Carson, J. S., Nelson, B. L., & Nicol, D. M. (2013). Discrete-Event System Simulation (5th edition). Pearson Higher Education.
Van Der Aalst, W. M. (2015). Business process simulation survival guide. In J. Vom Brocke and M. Rosemann, M. (Eds.) Handbook on Business Process Management 1: Introduction, methods, and information systems (pp. 337-370). Springer, Berlin, Heidelberg.