Applications of digital twins outside manufacturing
March 6, 2022
1925 words
10 minutes to read
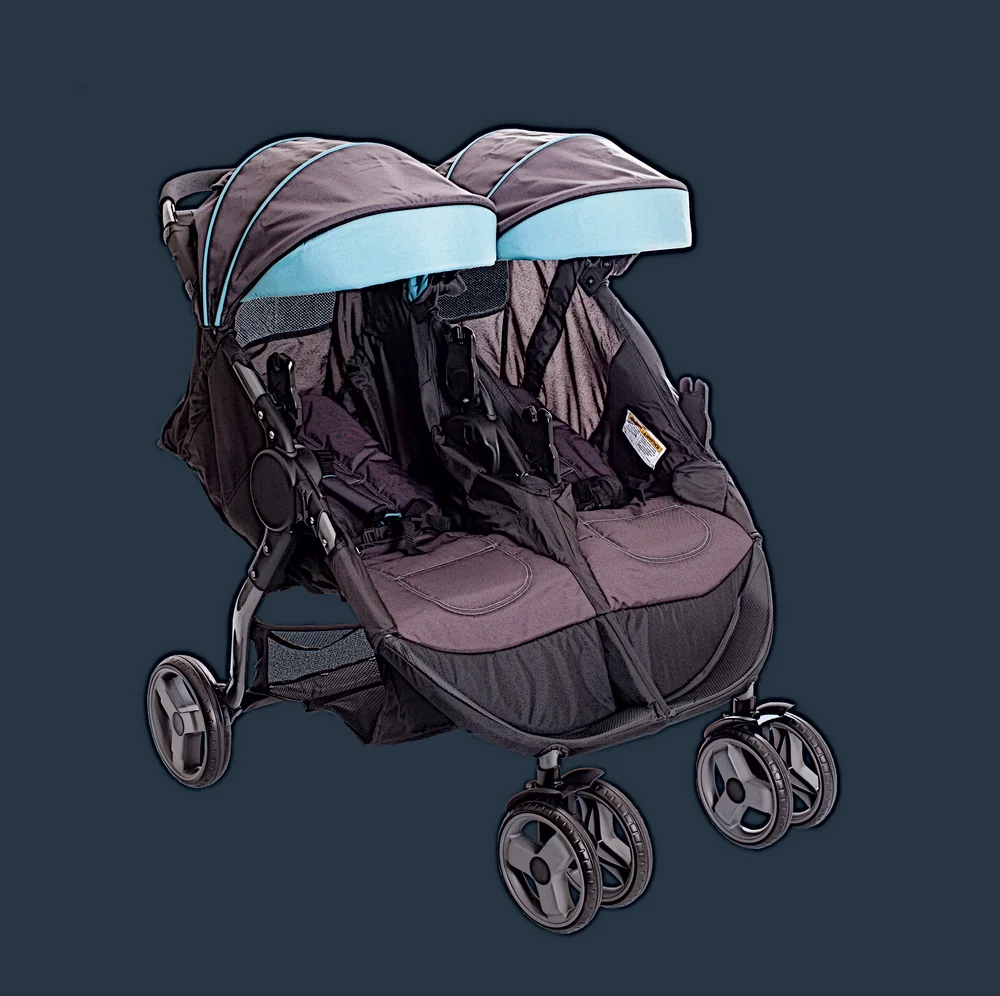
Do you need to test a prototype process in a safe environment before actually implementing it? Digital twins might be able to help!
With the increasing popularity of edge and IoT (Internet of Things) devices, the amount of data we access rises by the day. We now have so much real-world data that we can make near-perfect copies of many real-world objects and phenomena. The phrase digital twin was first coined by John Vickers, NASA’s chief technology officer. Later in 2003, Michael Grieves proposed the conceptual framework of a digital twin (Figure 1) with Vickers (Grieves and Vickers, 2017). They framed the concept as the interconnection of a physical product (reality) in combination with its digital representation (virtual).
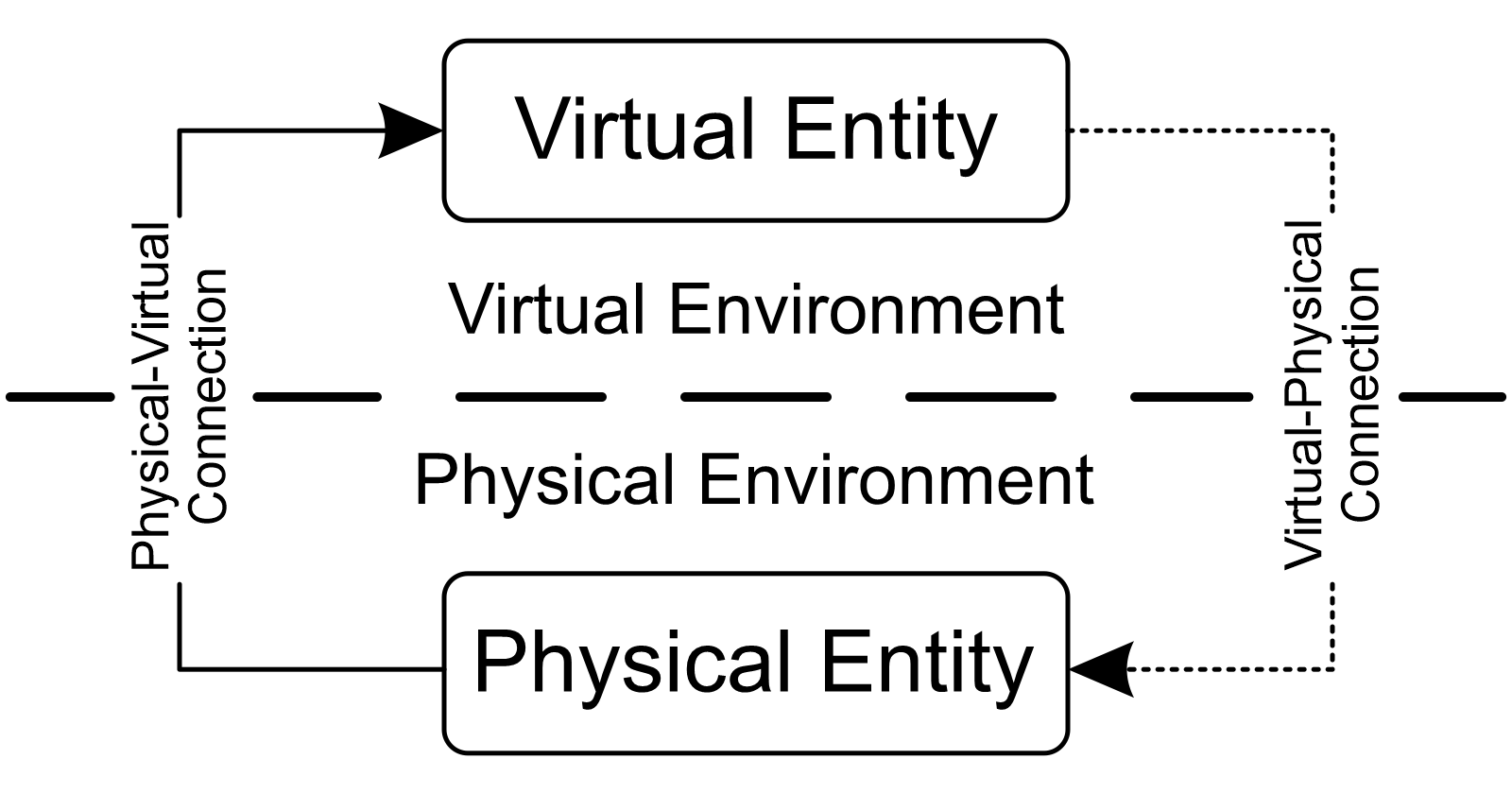
Digital twins are now being used in many industry sectors, (such as Aerospace and Defense, Automotive and Transportation Machine Manufacturing, Energy, and Utilities), to reduce downtime, increase cost savings, and improve customer satisfaction. However, many businesses are still missing out on the benefits of digital twins because they don’t understand how they can help them.
The increased focus on the growth of Industry 4.0 is stimulating the growth of the digital twin market. The digital twin concept facilitates increased virtual system-based design processes, permitting any equipment, technology, or system to more actively participate. Digital twin technology supports increased understanding of unique product features, performance, and potential faults on the virtual simulation model. The use of digital twins offers an accurate digital reproduction of the machine.
This post aims to clarify the uses and benefits of digital twins. Below, we are going to have a look at:
- What is a digital twin?
- What are the benefits of digital twins?
- What are the applications of digital twins outside manufacturing?
What is a digital twin?
A digital twin is a virtual copy of a physical object or process. Digital twins are designed to be the exact replicas of their real-world counterparts.
“Let us first define a digital twin. One vendor’s or customer’s definition of digital twin may vary drastically from another. They range from a simulation of a single physical component, predictive maintenance for a piece of equipment, to a full 3D virtual walkthrough of a factory with automated operations utilizing command and control procedures. What they all have in common is that digital twins form a digital representation of something in the physical world, updated with live data, and used to drive business outcomes. Based on these common elements, a digital twin is defined as a living digital representation of an individual physical system that is dynamically updated with data to mimic the true structure, state, and behavior of the physical system, which informs decisions that drive business outcomes.”
– Raj Devnath (30 NOV 2021) The Internet of Things on AWS – Official Blog, Introducing AWS IoT TwinMaker
The key characteristics of digital twins are as follows (Jones, et al., 2020):
- Digital twins can cover the entire lifecycle of a real-world object or system.
- Digital twins can be updated from real-time data.
- Digital twins help decision-making through reasoning, simulation, and machine learning.
Businesses can use digital twins at a very high level in two types of applications – prototyping and monitoring. We give a brief overview of these applications below.
Digital twins in prototyping
Products and processes can be tested by Digital twins before they are actually produced or implemented. This allows businesses to test ideas and tweak parameters safely and predictably.
In many situations, digital twins are far more cost-effective than real-world prototypes. With digital twins, businesses can test pretty much any parameter configuration without repeatedly making changes in real, physical objects or processes. Digital twins also let businesses figure out how changes can affect the long-term performance of the modeled object.
Digital twins in monitoring
Businesses can create digital twins to monitor the performance of already existing products. Digital twins can be fed real-time data collected from the sensory inputs of an object to reflect its current condition.
As far as monitoring is concerned, digital twins can help businesses:
- Monitor the performance of a product and ascertain that it meets key performance indicators.
- Make virtual changes to the product to identify potential routes for improvement.
- Detect irregularities in the product’s operation and make preemptive fixes.
What are the benefits of digital twins?
Digital twins offer the following benefits to businesses (Rossmann and Hertweck, 2022):
- Isolated, safe testing environment. With digital twins, enterprises do not need to change existing products or processes to test improvements. Because they are deployed in remote virtual environments, digital twins can’t affect the actual operations.
- Reduced product/process development costs. Businesses don’t need to produce actual products or implement processes to test them with digital twins. Enterprises can test different ideas quicker and with reduced costs.
- Reduced downtime. Real-time monitoring can be invaluable for predictive maintenance. By constantly testing different scenarios, businesses can detect issues before they rear their ugly heads. Enterprises can preemptively improve and fix their products, reducing downtime.
Digital twins vs simulation – which is better?
Digital twins sound a lot like simulation, so are they the same thing? Although there is an inevitable overlap between simulation and digital twins, they aren’t the same and have distinct features (Grieves, 2019).
Perhaps most importantly, simulations are typically focused on one specific process, while digital twins can incorporate entire environments with various processes. Therefore, digital twins are more complex and inclusive than simulations.
Another distinction is that simulations typically don’t use real-time data for calculations. In contrast, digital twins rely heavily on real-time sensory input for monitoring. Besides, thanks to a combination of real-time data and simulation, digital twins can predict how a product or process will respond to changes in its environment.
That said, simulation can be easier to design and implement because of its narrower focus. Simulation modeling may not be as broad as digital twins, but the implementation of digital twins often requires more research. Therefore, whenever possible, teams should go with simulation.
The applications of digital twins outside manufacturing
Digital twins are heavily associated with manufacturing, but they have found uses in many other industries. Any object or process can improve through measuring and monitoring within digital twins. We outline some of the most interesting and exciting applications of digital twins outside manufacturing below!
“Based on application, Automotive & Transportation are expected to be the most lucrative [market]. The rising use of digital twins for designing, simulation, MRO (maintenance, repair, and overhaul), production, and after service can be attributed to this growth. Automotive and transportation is one of the areas that will see significant growth in the post-COVID-19 period, as industry participants attempt to implement digital solutions for their end-to-end operations in order to reduce losses caused by the pandemic.”
– QY Research. (January, 2022) Global Digital Twin Market Insights and Forecast to 2028. Valuates Reports.
Datacenter design
Businesses can design corporate networks and data centers more efficiently with digital twins. As computer networks have grown more complex, testing and validating systems manually have become extremely challenging. Businesses can pretest a wide range of configurations for routing, automation, monitoring, and cybersecurity with digital twins. Companies can then seamlessly implement the best network configuration based on pretest results.
Planning aside, digital twins can also help assess network changes before they go into production.
Healthcare
Digital twins have found application in healthcare as well. Medical institutions can use digital twins to:
- Optimize their operational performance by testing different management, staffing, and patient care models. Model testing can help institutions reduce operating costs and eliminate functional bottlenecks.
- Keep track of patient health indicators to provide personalized care and improve treatment outcomes. More efficient operations mean more timely patient treatment, not to mention that they can, again, help institutions reduce costs.
Urban planning
Digital twin technology can be applied on much larger scales than separate institutions or data centers. One such area that can tremendously benefit from digital twins is urban planning. With digital twins, governments and city authorities can optimize any aspect of city operation, starting from traffic and emergency response and ending with construction and event organization.
Several cities worldwide are now using digital twins to improve their efficiency and fine-tune their urban design. Among these cities are Hong Kong, Singapore, and Rennes in France, which use Dassault Systèmes’ 3DEXPERIENCE platform to respond to urban challenges quickly.
Climate prediction
As climate change becomes an increasingly concerning problem for academic and political circles, digital twins can help researchers predict extreme weather changes and make informed, more sustainable decisions.
A notable project in this area is Destination Earth – a large-scale simulation of the Earth developed by the European Union. Destination Earth was launched in an effort to support the EU’s initiative to become climate-neutral by 2050. Destination Earth was designed to render Earth at a one-kilometer scale and leverage continuously updated data from climate, atmospheric, and meteorological sensors.
Retail and order fulfillment
Retail giants like Amazon deliver billions of packages each year. Such a logistical volume wouldn’t have been possible without meticulous planning and process optimization – things that can again be done with digital twins.
More specifically, digital twins can be used to test fulfillment pipelines, address bottlenecks, and intelligently combine human staff with robots. Ultimately, digital twins can help businesses in the retail sector increase their cost-effectiveness and improve customer satisfaction.
Next steps
Businesses can use digital twins in pretty much any industry. As long as you can build a sufficiently accurate copy of a real-world object or process, you can leverage digital twins to make improvements to it.
The subsequent question to “What are the Applications of Digital Twins Outside Manufacturing?” is “How should an enterprise deal with a multitude of digital twins in one facility? For example, how should an enterprise integrate lower-level detailed digital twins with a higher-level, more abstract digital twin? Moreover, how will these networks be managed if each digital twin is considered individually?
One theoretician suggested that digital twins could be combined into a structured network controlled by one single point of truth, called the Digital Twin of a System (Reiche, et al., 2021, September). This forbodes a fascinating challenge for working with multiple digital twins.
However, simulation by itself should not be ignored. Although a narrower concept, simulation can still be a powerful tool in many situations, like software delivery modeling. Simulation isn’t as all-encompassing as digital twins, but it can be much easier to implement. Inexpensive online courses could support jump-starting the team on this timely and useful concept:
References:
Grieves, M., & Vickers, J. (2017). Digital twin: Mitigating unpredictable, undesirable emergent behavior in complex systems. In Transdisciplinary Perspectives on Complex Systems (pp. 85-113). Springer.
Grieves, M. (2019). Virtually intelligent product systems: Digital and physical twins. In S. Flumerfelt, et al., (Eds). Complex Systems Engineering: Theory and Practice. American Institute of Aeronautics and Astronautics. p. 175-200.
Jones, D., Snider, C., Nassehi, A., Yon, J., & Hicks, B. (2020). Characterising the Digital Twin: A systematic literature review. CIRP Journal of Manufacturing Science and Technology, 29, 36-52.
Reiche, L. T., Gundlach, C. S., Mewes, G. F., & Fay, A. (2021, September). The Digital Twin of a System: A Structure for Networks of Digital Twins. In 2021 26th IEEE International Conference on Emerging Technologies and Factory Automation (ETFA) (pp. 1-8). IEEE.
Rossmann, A. & Hertweck, D. (2022). Digital Twins: A meta-review on their conceptualization, application, and reference architecture. In _Proceedings of the 55th Hawaii International Conference on System Science_s. http://hdl.handle.net/10125/79887