Aligning functional modeling with process improvement
January 9, 2021
1015 words
5 minutes to read
Last Updated: January 15, 2022
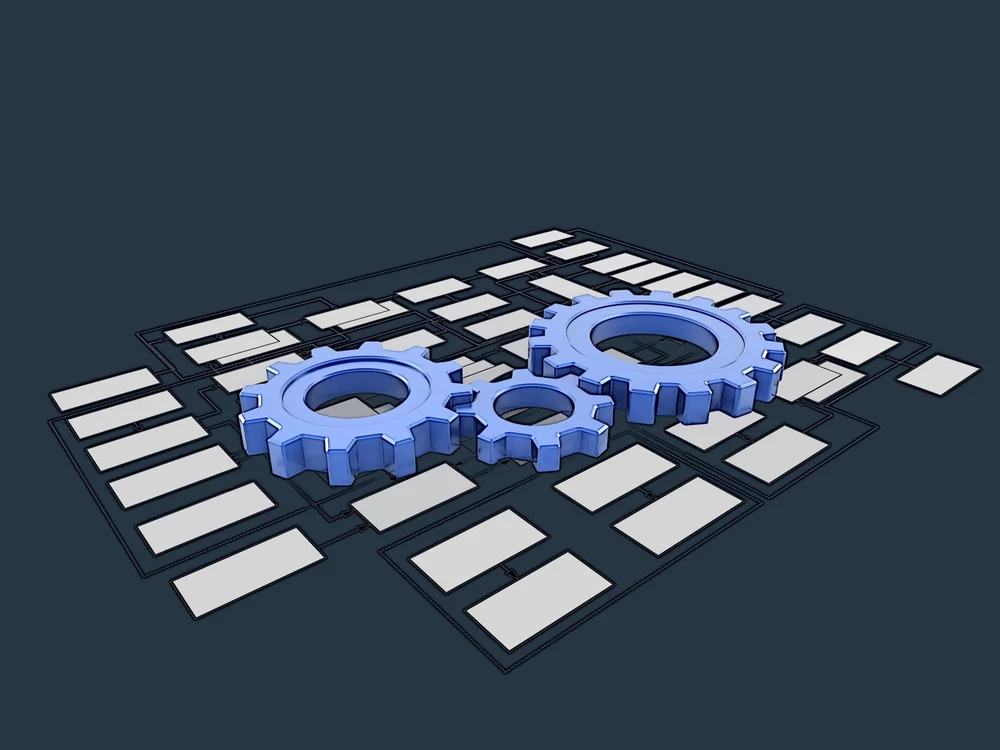
Functional modeling provides an excellent foundation for process improvement. By laying out all the processes within a system, and the flows between them, the team will be able to identify areas that the team can optimize. Conversely, the team can envision the complete current system and create a functional model that could become a ‘dream model’ - to achieve the same outcomes as your current model but with added value.
Read our post about Getting Started With Functional Modeling if you’re unsure how to create a model. To improve enterprise processes, two functional models will be necessary: your current model (“as is”) and your desired model (“to be”).
Which model should be created first?
Approach #1: Creating the desired functional model first
Starting with the process that is “to be” in the future encourages creativity, creates optimism about what the team can accomplish, and shapes/biases the thinking about future modeling phases. For these reasons, starting with the process as it should be in the future is often the best approach.
Approach #2: Creating the current functional model first
The “as is” process may receive less fanfare and excitement than the “to be” process. However, this accurate understanding and representation of how the organization operates is a prerequisite for a successful process improvement project.
When creating the current or “as is” functional model, team members should leverage interviews and other direct work with frontline workers, experts, and software systems of record. Collect lists of verb-noun phrases, which will serve as the function models in a larger, coupled component model.
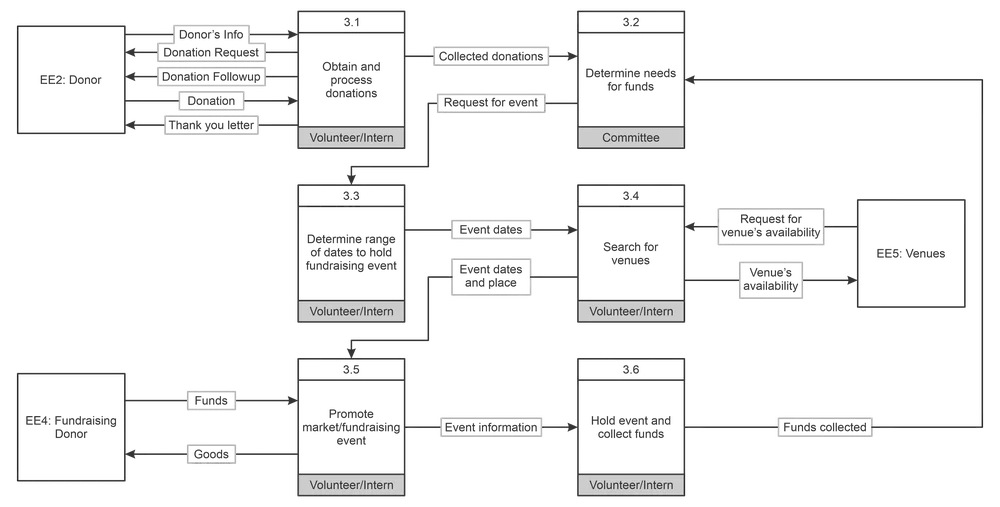
Moving from the current functional model to the desired functional model
Using an incremental, controlled approach, teams should move towards the “to be” process from the “as is” process. If the team immediately attains the “to be” process, the team may not have been creative or rigorous enough in the systems design process. Instead, impactful process improvements require significant changes that should be rolled out incrementally.
Consider a simple rollout strategy of:
- Measure
- Analyze
- Improve
Furthermore, each Measure, Analyze, Improve (MAI) cycle should be followed by a control and stabilization phase (Flifel, et al., 2017). This D(MAI)C quality strategy is part of the Six Sigma initiative that can be used with lean principles, a derivate of manufacturing optimization that can be applied to software development. D stands for Define and C represents the Control step.
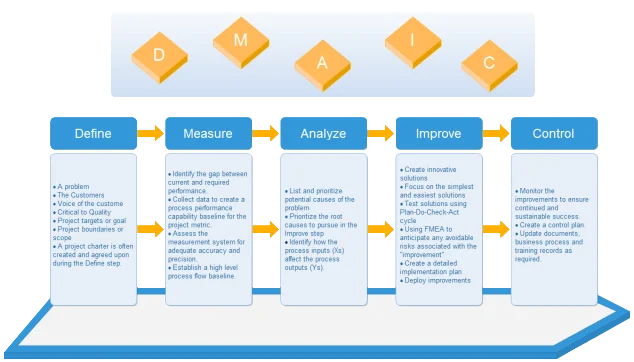
Many obstacles emerge in organizations when trying to apply Six Sigma, especially the DMAIC method:
- Senior management does not commit to the investment of time and resources;
- Six Sigma green belt (GB) and black belt (BB) certified personnel are expensive to hire and retain; and
- By the very nature of their organization, enterprises tend to deflect any significant changes.
In a study of the service industry by Purba (July 2019), most enterprises partially implemented the method, abandoning the execution of the complete DMAIC steps. Moreover, performing the DMAIC steps in the recommended sequence was also a critical success factor.
An example: Improving web app security
Consider the steps in an initiative to improve web application security:
- The team measures and analyzes the current systems and, in doing so, identifies a need for automated security and compliance checking;
- The team then improves the process through the integration of these products and DevSecOps principles;
- A control and stabilization phase should follow, where variation is reduced and the stable, reliable process emerges; and
- After the resulting data suggests that control and stabilization have occurred, the team can implement the next MAI cycle to get another step closer to the “to be” process.
Tips for modeling towards process improvement
Tip #1 - Keep an eye out for non-value-added activities
When modeling processes, keep an eye out for “red flags” of non-value-added activities:
- From the customer’s point of view, does the activity provide value?
- Is an activity truly necessary if it does not provide value?
- How can teams be enabled and approved to eliminate non-value-added activities?
Seven categories of waste are typically associated with non-value-added activities Carreira (2005, p. 68):
- Activity resulting from a rejected product,
- Overproduction,
- Process,
- Transport,
- Unnecessary inventory,
- Unnecessary motion, and
- Wait time.
Arafeh (2015, p. 212) described “Non-value-added refers to an activity that consumes time (people expense), material, and/or space (facilities expense), yet does not physically advance the product or increase its value” (see Figure 2 for an example of value-added vs. non-value-added).
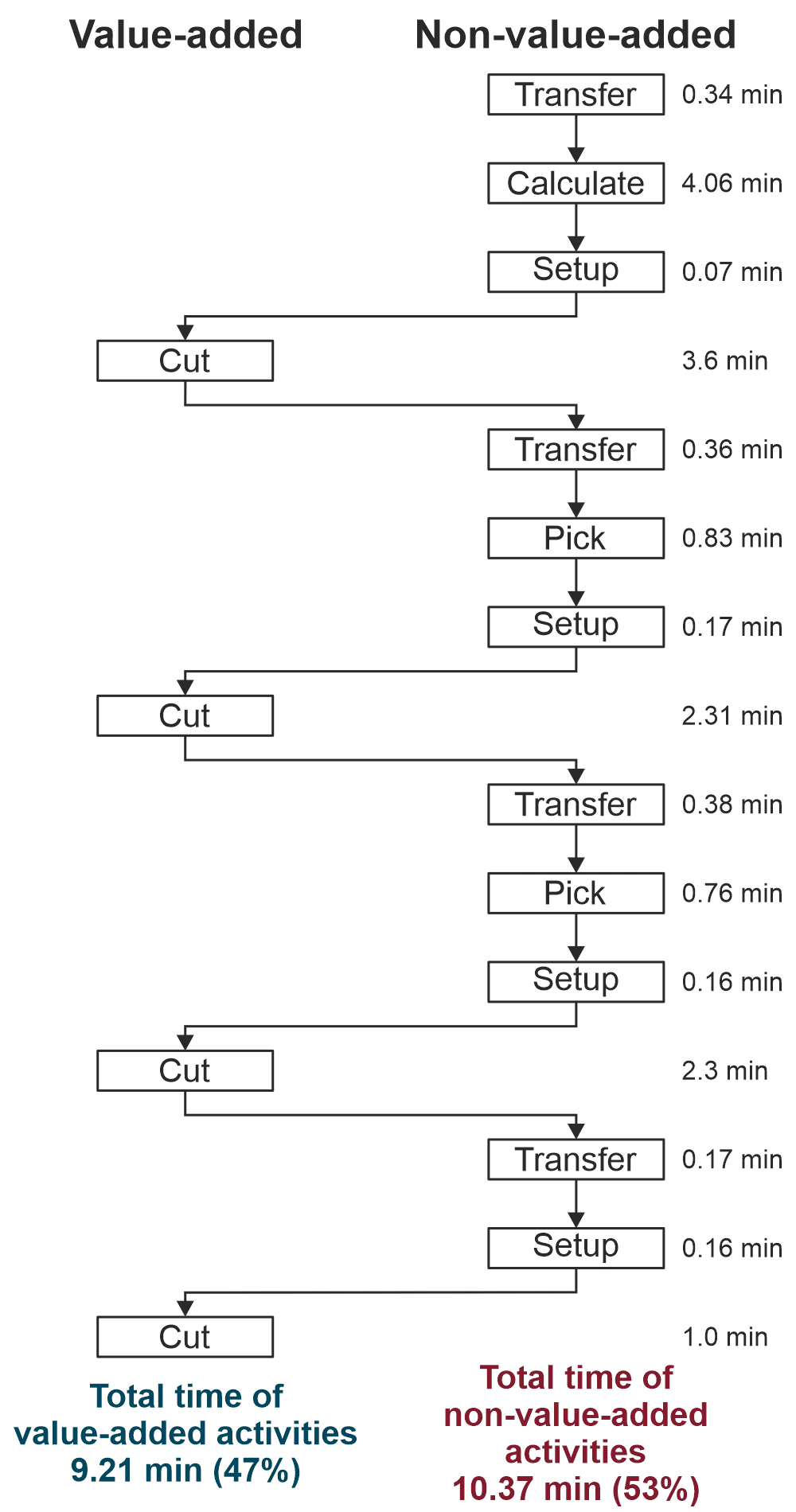
Tip #2 - Model multiple flow types
Individuals, teams, and organizations may naturally focus on particular types of “flow.” However, a holistic approach with multiple perspectives will typically lead to better insights and process improvements. As a start, consider the flows of information, product, material, and cash.
Tip #3 - Identify opportunities for simplification and control
Process improvement is not just about integration and automation. Simplification and control could be the areas of a higher return on investment. “Control” here is meant in the low-variation process sense, not in the bureaucracy and centralized power sense.
Next steps
To sample the DMAIC Approach in Lean Six-Sigma, why not ask one or two of your team members to enroll (for free) and complete the Six Sigma and the Organization (Advanced) Course from the University System of Georgia? This learning could be the start of something precious for the enterprise.
References:
Arafeh, (2015). Combining Lean Concepts & Tools with the DMAIC Framework to Improve Processes and Reduce Waste. American Journal of Operations Research, 5, 209-221.
Carreira, B. (2005). Lean manufacturing that works: Powerful tools for dramatically reducing waste and maximizing profits. AMACOM Div of the American Management Association.
Flifel, A. F., Zakić, N., & Tornjanski, A. (2017). Identification and selection of Six Sigma projects. Journal of Process Management, New Technologies, 5(2), 10-17.
Purba, H. H. (July 2019). Consistency analysis of implementation define, measure, analyze, improve, and control (DMAIC) steps on six sigma method in service industries sector: A literature review. International Journal of Scientific Research Engineering & Technology (IJSRET) 8(7), 373-379.